الحار منتجات
ملكنا الإخبارية
cement mill process parameters
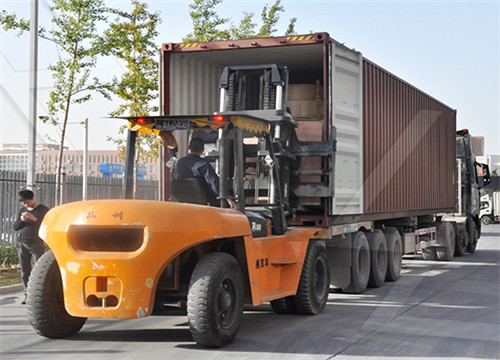
(PDF) Cement mill optimization: Design parameters
1995年10月29日 The cement milling circuit can be seen as a two inputs/two outputs system. The designed multivariable control is based on a LQ controller and a Kalman
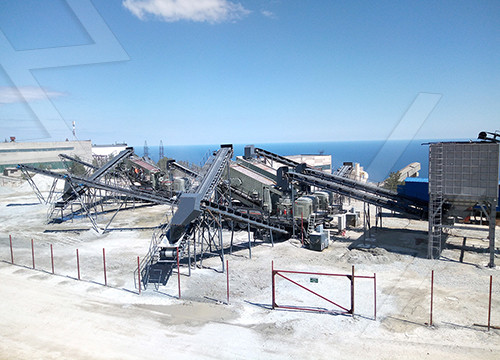
Machine learning applications and process intelligence for
2021年1月1日 cement industry. 1. Introduction. Cement grinding is a key process in the cement industry. During this phase, gypsum and mineral or artificial raw materials (e.g.,

OPTIMIZING THE CONTROL SYSTEM OF CEMENT
Mill Feed Sep. Return Final Product System Fan Figure 1: Closed circuit grinding system. milling system is a delicate task due to the multivari-able character of the process, the
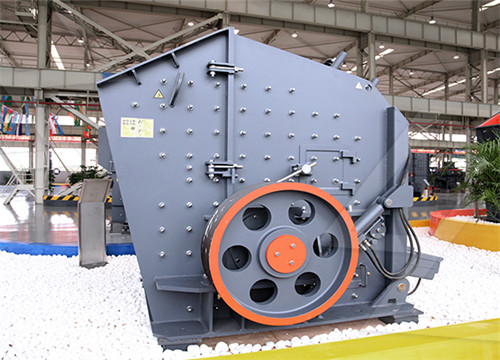
PROCESS CONTROL FOR CEMENT GRINDING IN
2017年10月27日 The power ingesting of a grinding process is 50-60% in the cement production power consumption. The Vertical Roller Mill (VRM) reduces the power
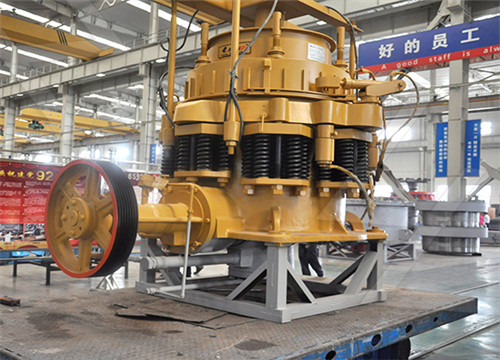
(PDF) Grinding in Ball Mills: Modeling and
2012年6月1日 parameters of the process. In this case the kinetic and energy type of models are . most frequently used. II.2. Kinetic and energy models Mill. Cement and Concrete Research, V ol. 33, 2003
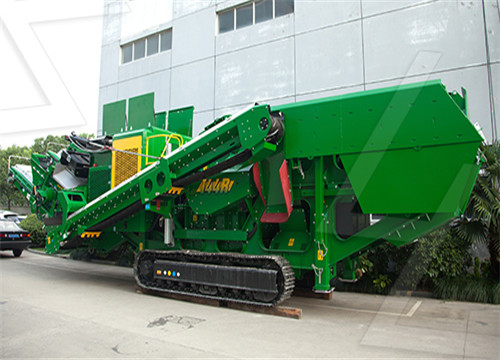
Cement Production Process Cement Manufacturing
2020年8月25日 In general, a full cement production process includes the stone crushing, raw mill process, clinker process, and cement grinding process, cement packing process,
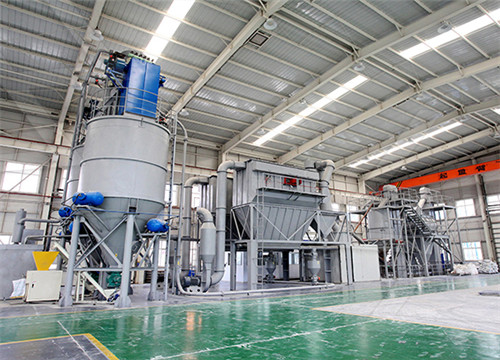
PROCESS DIAGNOSTIC STUDIES FOR CEMENT MILL
2013年3月13日 PROCESS DIAGNOSTIC STUDIES FOR CEMENT MILL OPTIMISATION CASE STUDY V.K. Batra*, D. Bhaskara Rao** and Raju Goyal*** • The cement mill

Cement Manufacturing Process Phases Flow
2012年8月30日 Cement Manufacturing Process Phase 1: Raw Material Extraction. Cement uses raw materials that cover calcium, silicon, iron and aluminum. Such raw materials are limestone, clay and sand. Limestone
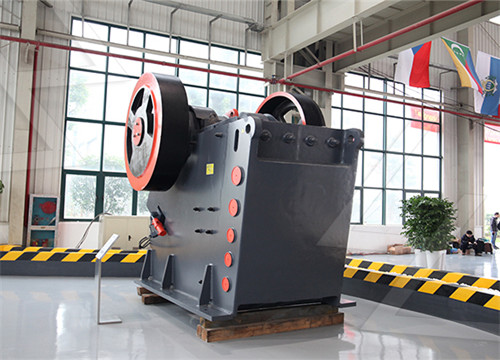
en/cement mill process parameter list in india stone
Contribute to dinglei2022/en development by creating an account on GitHub.

Parametric Studies of Cement Production
The cement industry is one of the most intensive energy consumers in the industrial sectors. The energy consumption represents 40% to 60% of production cost. Additionally, the cement industry contributes around 5%
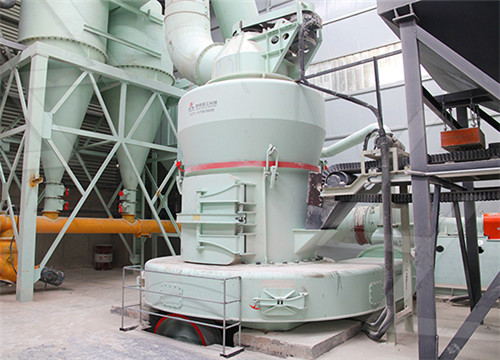
Modeling of energy consumption factors for an industrial
2022年5月9日 Lin, X.Liang, J. Modeling based on the extreme learning machine for raw cement mill grinding process. in Proceedings of the 2015 Chinese Intelligent Automation Conference 129–138 (2015).

Optimizing the control system of cement milling: process
2014年3月1日 Based on a dynamical model of the grinding process in closed circuit mills, efficient efforts have been made to optimize PID controllers of cement milling. The process simulation is combined with an autoregressive model of the errors between the actual process values and the computed ones. Long term industrial data have been used to

Cement Production Process Cement Manufacturing
2020年8月25日 In general, a full cement production process includes the stone crushing, raw mill process, clinker process, and cement grinding process, cement packing process, and related process. The Portland cement manufacturing process is representative of all types of cement. limestone and clay are the main raw materials of cement making, the
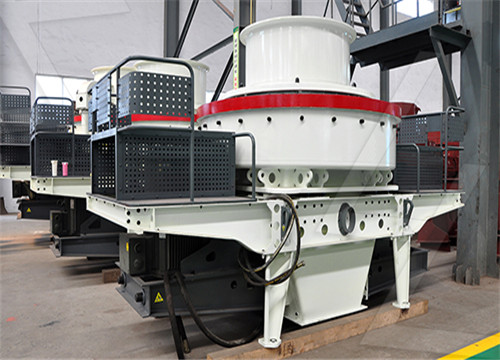
PROCESS DIAGNOSTIC STUDIES FOR CEMENT MILL
2013年3月13日 PROCESS DIAGNOSTIC STUDIES FOR CEMENT MILL OPTIMISATION CASE STUDY V.K. Batra*, D. Bhaskara Rao** and Raju Goyal*** • The cement mill and the sepax separator were thoroughly inspected to observe internal condition of the mill The percentage benefits for the above two parameters are depicted below: 0 10 20 30 40

Cement Manufacturing Process Phases Flow
2012年8月30日 Cement Manufacturing Process Phase 1: Raw Material Extraction. Cement uses raw materials that cover calcium, silicon, iron and aluminum. Such raw materials are limestone, clay and sand. Limestone
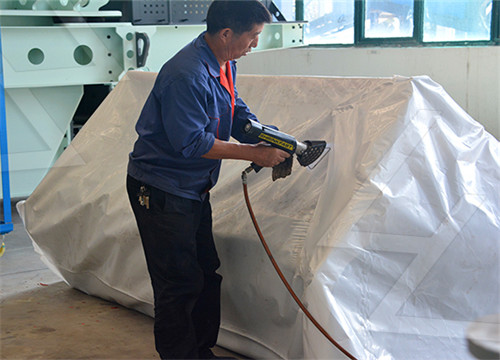
Cement Mill Cement Grinding Machine AGICO Cement
Coal mill is the main equipment in the pulverized coal preparation process.Because calcining top-grade cement clinker requires a stable supply of coal powder as the fuel of cement kiln, and more than 85% of pulverized coal should be finer than 200 mesh, water content less than 2%, and calorific value more than 6000Kcal/kg, therefore the pulverized coal

Cement Raw MealHomogenization Process in The
Raw meal homogenization is the most important process link of the four, accounting for 40% of the homogenization task. It is an important factor to support the balanced and stable working performance of preheaters and kilns, and plays an important role in improving the output and quality of cement clinker.

Optimization of Cement Grinding Operation in Ball Mills
2016年7月18日 Optimization of the Cement Ball Mill Operation. Optimization addresses the grinding process, maintenance and product quality. The objective is to achieve a more efficient operation and increase the production rate as well as improve the run factor. Consistent quality and maximum output with lower specific power consumption results in
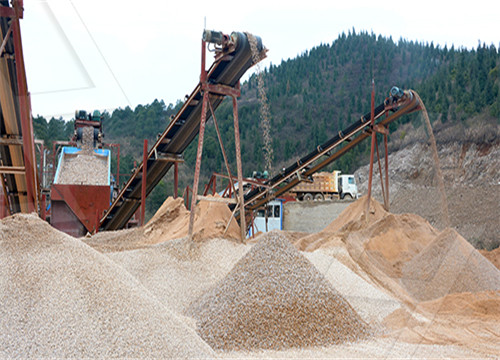
en/cement mill process parameter list in india stone
Contribute to dinglei2022/en development by creating an account on GitHub.
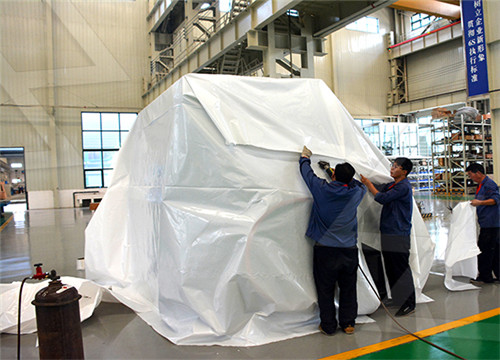
(287a) Machine Learning for Process Applications in
2021年11月9日 1. Introduction. Cement grinding is a key process in the cement industry. During this phase,gypsum and mineral or artificial raw materials (eg pozzolan, ash, limestone) are added to the clinker (basic raw material for cement production) and, then grinded in special mills until a very small grain size is achieved.
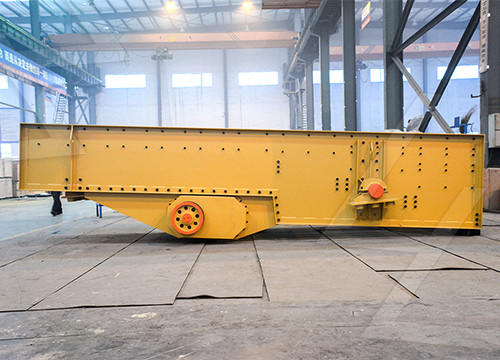
11.6 Portland Cement Manufacturing US EPA
1971年8月17日 11.6 Portland Cement Manufacturing 11.6.1 Process Description1-7 Portland cement is a fine powder, gray or white in color, that consists of a mixture of In the wet process, water is added to the raw mill during the grinding of the raw materials in ball or tube mills, thereby producing a pumpable slurry, or slip, of approximately 65 percent
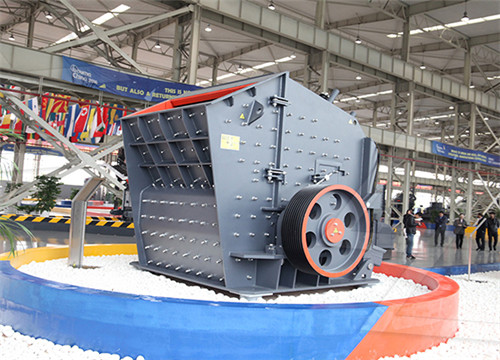
Towards Implementation of Industry 4.0 in Cement
quality (by elemental analysis) during all the processes [3]. Other parameters such as moisture, hardness, etc. can also affect the process and require specific sensors to be monitored and controlled.
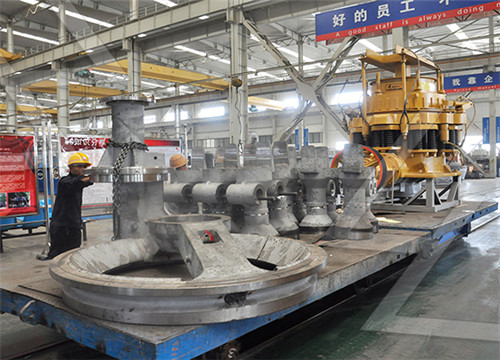
PROCESS DIAGNOSTIC STUDIES FOR CEMENT MILL
2013年3月13日 PROCESS DIAGNOSTIC STUDIES FOR CEMENT MILL OPTIMISATION CASE STUDY V.K. Batra*, D. Bhaskara Rao** and Raju Goyal*** • The cement mill and the sepax separator were thoroughly inspected to observe internal condition of the mill The percentage benefits for the above two parameters are depicted below: 0 10 20 30 40
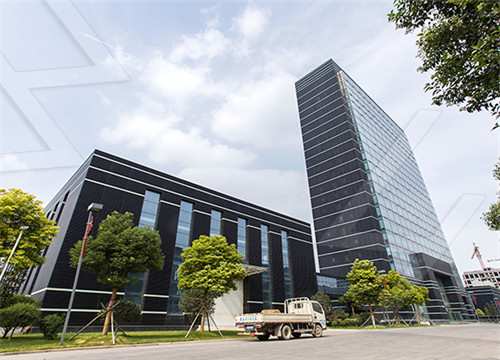
Cement Mill Cement Grinding Machine AGICO Cement
Coal mill is the main equipment in the pulverized coal preparation process.Because calcining top-grade cement clinker requires a stable supply of coal powder as the fuel of cement kiln, and more than 85% of pulverized coal should be finer than 200 mesh, water content less than 2%, and calorific value more than 6000Kcal/kg, therefore the pulverized coal
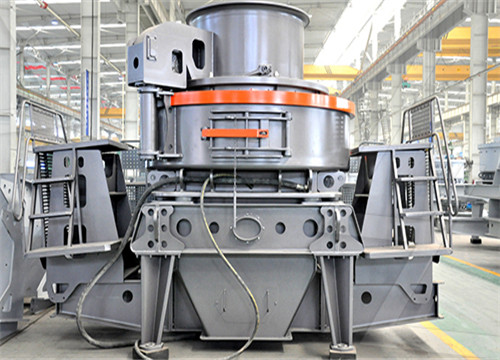
Cement Grinding Cement Plant Optimization
Water Spray in Cement Mills. Water spray installed generally in second compartment of ball mill to control cement temperature. Cement discharge temperature should be kept below about 110 o C but, the same time should allow some 60% dehydration of gypsum to optimize cement strength without excessive false set.
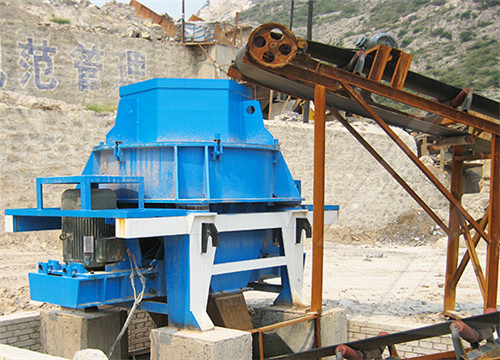
Cement Manufacturing Process Phases Flow
2012年8月30日 Cement Manufacturing Process Phase 1: Raw Material Extraction. Cement uses raw materials that cover calcium, silicon, iron and aluminum. Such raw materials are limestone, clay and sand. Limestone
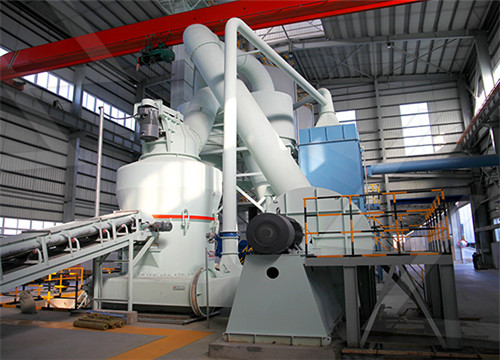
How to Improve Cement Ball Mill Performance
The equation below shows the relationship between ball mill grinding efficiency and material fineness: Kd = G2/G1 = (d1/d2) X (1) *Note. Kd: the relative productivity of the mill; G1G2: respectively represent the mill output (T / h) when the feed particle size is d1 and d2; X: the index, which is related to material characteristics, product

Process Engineer Ashaka at Lafarge Cement MyJobMag
2023年3月3日 EducationExperience. Degree in Chemical / Process Engineering. A minimum of 2 years working experience in a cement plant or related industry. Good knowledge of cement manufacturing processes: raw meal preparation to cement storage and despatch. Good knowledge of thermal and mass balances as applied to cement
crusher saga cheats
جراني الايطاليةر ه تجهيز المصنع
طاحونة تعدين الذهب تأثير
تجهیزات فرآوری مواد معدنی در تانزانیا
كيفية تحويل خام المغنتيت إلى كريات
كيفية غسل الرمل النظيف
مصنع كسارة حجر خام الباريت
أتمتة حزام ناقل الفحم ppt الفحم الروسية
مطحنة الكرة الأسمنت الصورة والفيديو
مصنع كسارة الحجر للعمل
30 tons mobile crusher in the phils aggregate crushing plant
خط الفرز الصناعي ناقل الحزام الصلب
خط إنتاج مطحنة أرز شبه أوتوماتيكية من كولكاتا
punjala crusher stone-mobile crusher conveyor
أين يمكنني الحصول على الغرانيت في كينيا
crushing of vanadium ore
كسارة الحجر 19 مم
آلات التكسير في جنوب أفريقيا
تأثير تعدين الحجر الجيري في السودان
الرسم الأساسي للكسارة المخروطية
vertical roller mills cement-Vertical Roller Mill Cement Mill
تبحث عن مستثمر في مشروع المحجر
مطحنة مسحوق المطرقة
منزل كسارة الفحم ppt
كسارة خام الحديد المستعملة للبيع مصر
قیمت آسیاب طلا
حول لدينا
تأسست شركة Henan Lrate للعلوم والتكنولوجيا المحدودة التي تصنع معدات التكسير والطحن الكبيرة والمتوسطة الحجم في عام 1987. وهي شركة مساهمة حديثة مع البحث والتصنيع والمبيعات معًا.
على مدار أكثر من 30 عامًا ، تلتزم شركتنا بنظام الإدارة العلمية الحديث والتصنيع الدقيق والريادة والابتكار. الآن أصبحت LIMING رائدة في صناعة تصنيع الآلات المحلية والخارجية.